Table of Contents
Are you struggling to ensure the accuracy of your total station measurements? This guide will cover essential verification techniques for total station accuracy, focusing on proper calibration, setup procedures, and error identification. By mastering these methods, you'll improve the precision of your building information modeling projects and enhance your ability to use this powerful tool effectively. Learn how to leverage optics, remote control, and trigonometry principles to achieve optimal results and boost your confidence in field data collection.
Master Fundamental Concepts of Total Station Accuracy
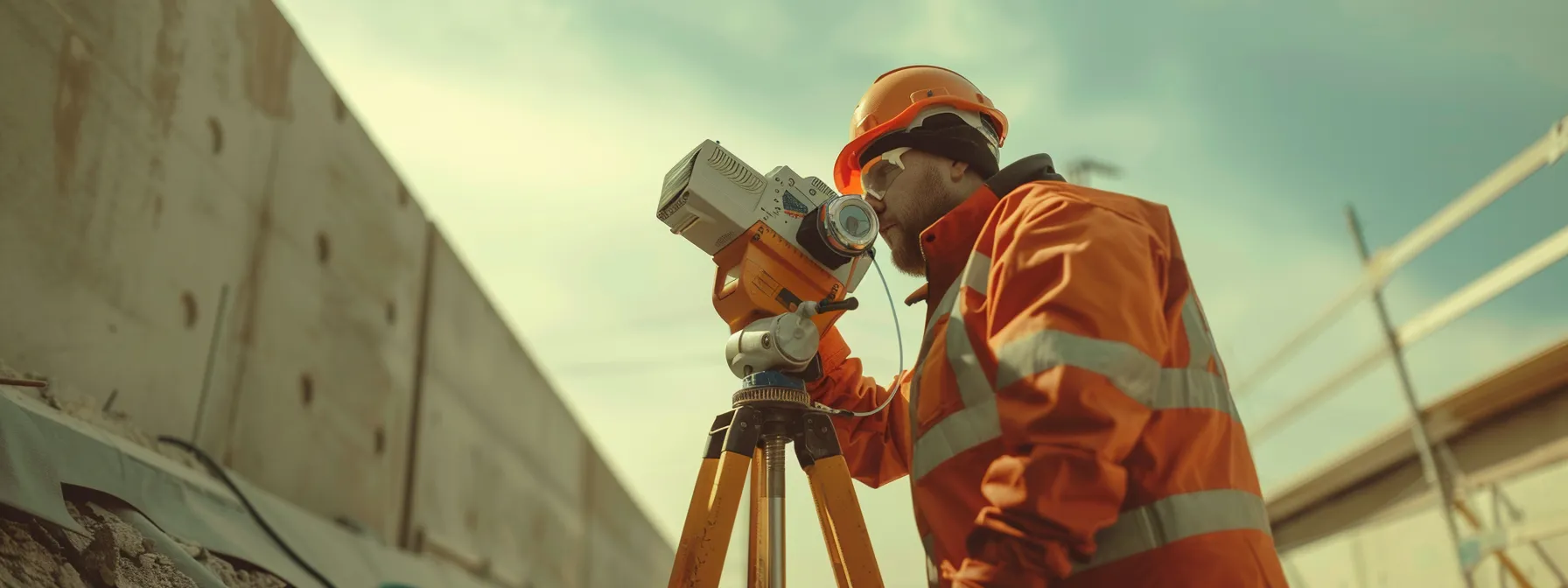
Mastering total station accuracy involves understanding key concepts. These include angular and distance measurement principles, instrument specifications, atmospheric corrections, leveling, prism constants, and calibration. Each aspect plays a crucial role in ensuring precise measurements across various areas, from robotics to geographic information systems. By grasping these fundamentals, surveyors can harness the full potential of total station technology and its beam-based measurement capabilities.
Comprehend Angular and Distance Measurement Principles
Understanding angular and distance measurement principles is crucial for achieving high accuracy with total stations. These instruments use precise optics and laser technology to measure angles and distances, forming the foundation of surveying workflows. By comprehending these principles, surveyors can optimize their use of total stations for various applications, including topography mapping and construction layout.
Angular measurements rely on the instrument's ability to determine horizontal and vertical angles accurately. Modern total stations employ electronic theodolites with digital encoders to measure angles with remarkable precision. This technology, combined with proper leveling of the instrument on its tripod, ensures reliable angular data for complex surveying tasks.
Distance measurements in total stations often utilize Electronic Distance Measurement (EDM) technology, which may include laser scanning or LiDAR capabilities. These systems emit a beam of light that reflects off a prism or target, allowing the instrument to calculate distances based on the time it takes for the signal to return. Understanding the principles behind these measurements helps surveyors account for atmospheric conditions and other factors that can affect accuracy.
Understand Instrument Specifications and Tolerances
Understanding instrument specifications and tolerances is crucial for engineers and surveyors using total stations. Leica Geosystems, a leading manufacturer, provides detailed information on their devices' accuracy limits for distance measurements and angular precision. These specifications help professionals determine if a particular instrument meets their project requirements.
Tolerance levels vary depending on the total station model and its intended applications. For instance, high-precision instruments used in engineering projects may have tighter tolerances compared to those used for general surveying. It's essential to consider factors such as measurement range, accuracy over distance, and environmental conditions when interpreting specifications.
Modern total stations often incorporate advanced features like Bluetooth connectivity, which can impact measurement accuracy. Engineers must understand how these technologies interact with the instrument's core functions and account for any potential sources of error. Regular calibration and verification procedures help ensure that the total station maintains its specified accuracy throughout its operational life.
Learn About Atmospheric Corrections and Their Impact
Atmospheric corrections play a crucial role in maintaining total station accuracy, especially when using laser technology for distance measurements. Temperature, pressure, and humidity affect the speed of light, impacting the precision of infrared EDM systems commonly used in total stations for infrastructure projects.
Modern total stations equipped with advanced microprocessors can automatically apply atmospheric corrections based on sensor data. These corrections are essential for maintaining accuracy across varying environmental conditions, particularly when measuring slopes or conducting long-range surveys in challenging terrains.
Surveyors must understand how to input atmospheric parameters manually when automatic corrections are unavailable. This knowledge ensures accurate measurements even in areas with rapidly changing weather conditions, ultimately leading to more reliable data for construction and engineering projects. Regular calibration of the total station's atmospheric sensors, along with proper maintenance of the battery charger, contributes to consistent performance in the field.
Recognize the Importance of Leveling and Centering
Proper leveling and centering of a total station are fundamental to achieving high accuracy in surveying and construction projects. The theodolite component of the instrument relies on precise leveling to ensure accurate angular measurements, while centering over a known point establishes the instrument's position in relation to the survey area. These critical steps lay the foundation for reliable data collection and improved productivity in various fields, including archaeology and satellite-based positioning.
Surveyors use a combination of bubble levels and electronic compensators to level the total station's telescope and base. This process ensures that the vertical axis of the instrument is truly perpendicular to the horizontal plane, minimizing errors in both horizontal and vertical angle measurements. Accurate leveling is particularly crucial when working on uneven terrain or in areas with limited visibility, where even small deviations can significantly impact the final results.
Centering the total station over a known point involves aligning the instrument's vertical axis with a specific ground mark or survey monument. This alignment establishes the instrument's position within the survey network and enables precise coordinate calculations. Modern total stations often incorporate laser plummets or optical plummets to facilitate quick and accurate centering, enhancing overall efficiency in field operations.
Grasp the Effects of Prism Constants on Measurements
Prism constants play a crucial role in total station accuracy, particularly in construction projects. These constants account for the optical and physical characteristics of prisms, ensuring precise distance measurements. Surveyors must input the correct prism constant into the total station's software to avoid systematic errors that can accumulate over large distances.
Different prism types, such as those used with Nikon instruments, have varying constants. Manufacturers typically provide these values, but surveyors should verify them through calibration procedures. Understanding how prism constants affect measurements allows professionals to select the most appropriate prism for specific tasks, optimizing accuracy in challenging construction environments.
The tribrach, which connects the total station to its support, can also influence prism constant effects. Proper maintenance and adjustment of the tribrach ensure consistent prism orientation, reducing errors in distance measurements. By grasping these concepts, surveyors can enhance the overall accuracy of their total station setups and improve the reliability of construction layout data.
Explore the Role of Calibration in Maintaining Accuracy
Calibration plays a crucial role in maintaining the accuracy of total stations for data collection in building projects. Regular calibration ensures that the instrument's angular and distance measurements remain within specified tolerances, providing reliable results for 3D scanning and volume calculations. Surveyors must perform calibration checks at specified intervals to detect and correct any deviations in the instrument's performance.
The calibration process typically involves measuring known reference points and comparing the results to established values. This procedure helps identify errors in the total station's optics, electronics, and mechanical components. For building applications, calibration becomes especially critical when working on large-scale projects where small errors can compound over long distances.
Modern total stations often incorporate built-in calibration routines accessible through the instrument's computer interface. These automated processes guide users through a series of measurements to verify and adjust the instrument's parameters. By maintaining a consistent calibration schedule, surveyors can ensure their total stations deliver accurate data for various applications, from basic site layouts to complex 3D modeling of structures.
Perform Regular Calibration to Ensure Total Station Accuracy
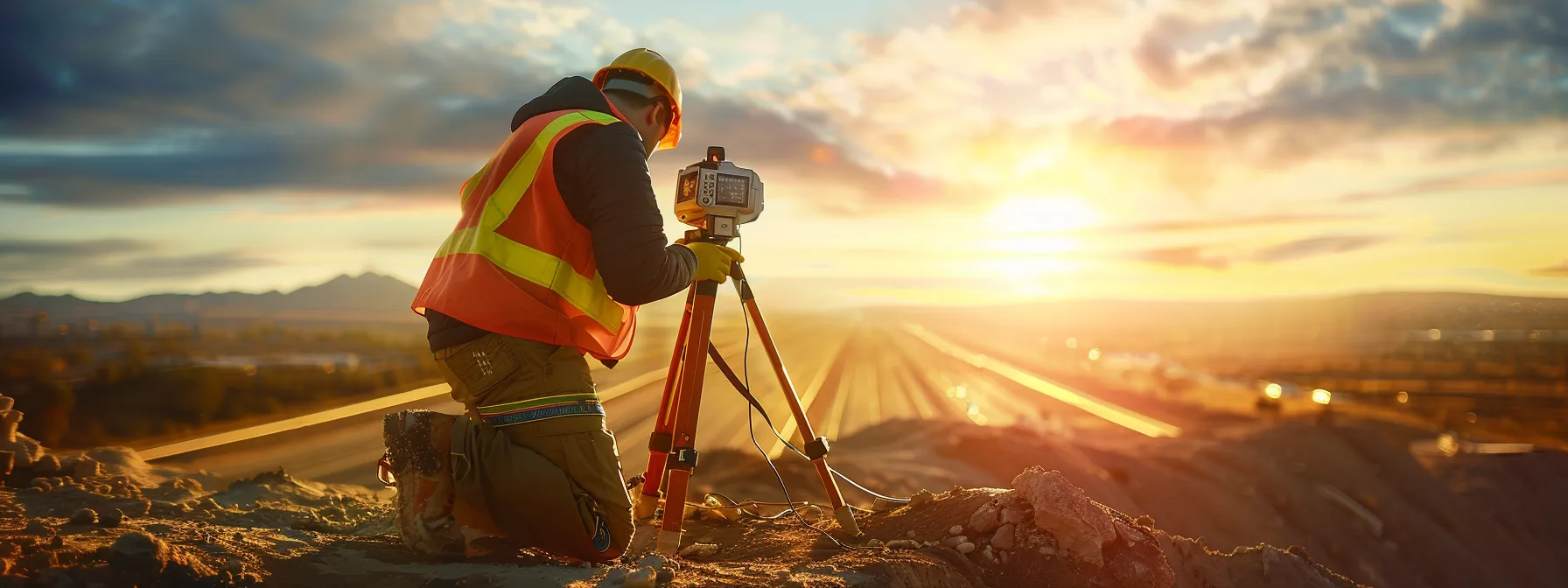
Regular calibration is crucial for maintaining total station accuracy. This process involves scheduling routine checks, utilizing proper equipment, following standard procedures, recording data, adjusting settings, and verifying accuracy in the field. By adhering to these practices, surveyors can ensure their total stations, including budget-friendly models with infrared technology, deliver precise measurements for various applications, even when using mobile apps for data collection.
Schedule Routine Calibration at Recommended Intervals
Civil engineers and surveyors should schedule routine calibration for their total stations at intervals recommended by manufacturers like Topcon. These regular checks ensure the instrument maintains its accuracy for measuring angles and distances, crucial for precise measurements in construction and surveying projects. Adhering to a consistent calibration schedule helps identify and correct any deviations in the instrument's performance before they impact project outcomes.
The frequency of calibration depends on several factors, including the total station's price range, usage intensity, and environmental conditions. High-end models may require less frequent calibration compared to budget-friendly options, but all instruments benefit from regular checks. Civil engineers should consider implementing a calibration schedule that aligns with project milestones or seasonal changes to maintain optimal performance throughout the year.
Modern total stations, including those compatible with Android devices for data collection, often feature built-in calibration routines. These automated processes guide users through a series of measurements to verify and adjust the instrument's parameters. By incorporating these routines into their regular maintenance schedule, civil engineers can ensure their total stations deliver accurate angular and distance measurements consistently, even in challenging field conditions.
Utilize Proper Calibration Equipment and Facilities
Utilizing proper calibration equipment and facilities is crucial for maintaining total station accuracy in surveying. Surveyors should invest in high-quality calibration tools, such as precision targets and reference benchmarks, to ensure reliable measurements. These tools, while potentially impacting the list price of the total station package, are essential for accurate data collection and 3D modeling.
Calibration facilities should provide a stable environment with controlled temperature and humidity to minimize external influences on measurements. Surveyors should establish dedicated calibration areas within their offices or utilize specialized calibration laboratories. This approach ensures consistent and reliable results, particularly for high-precision surveying tasks that require accurate distance and angular measurements.
Regular maintenance of calibration equipment is essential for preserving total station accuracy. Surveyors should follow a strict maintenance schedule and keep detailed records of all calibration activities. This practice helps identify trends in instrument performance and facilitates timely adjustments, ensuring the total station consistently delivers accurate data for various surveying applications:
- Establish a dedicated calibration area
- Invest in high-quality calibration tools
- Maintain a controlled environment for calibration
- Keep detailed records of calibration activities
- Regularly inspect and maintain calibration equipment
Follow Standard Procedures for Instrument Calibration
Following standard procedures for instrument calibration is crucial for maintaining the accuracy of Robotic Total Stations. Surveyors should adhere to manufacturer-specified guidelines, which typically involve a series of precise measurements and adjustments. These procedures ensure that the instrument's angular and distance measurements remain within acceptable tolerances, guaranteeing reliable data for various surveying applications.
Calibration procedures for Robotic Total Stations often include checks for horizontal and vertical angles, as well as distance measurements. Surveyors should perform these checks in a controlled environment, using known reference points and targets. By consistently following these standardized procedures, professionals can identify and correct any deviations in the instrument's performance before they impact project outcomes.
Regular calibration of Robotic Total Stations also involves verifying the instrument's compensator, optical plummet, and electronic distance measurement (EDM) system. Surveyors should document each step of the calibration process, recording initial readings, adjustments made, and final results. This documentation serves as a valuable reference for tracking the instrument's performance over time and ensuring its continued accuracy in the field.
Record and Analyze Calibration Data for Consistency
Recording and analyzing calibration data for consistency is crucial for maintaining total station accuracy. Surveyors should document each calibration session, including date, time, environmental conditions, and specific measurements taken. This detailed record-keeping allows for trend analysis and early detection of potential issues with the instrument's performance.
Consistency in calibration data indicates the reliability of the total station over time. By comparing results from multiple calibration sessions, surveyors can identify any gradual shifts in the instrument's accuracy. This information helps determine if more frequent calibrations or repairs are necessary to maintain optimal performance in the field.
Modern calibration software often provides tools for data analysis and visualization. These features enable surveyors to generate reports and graphs that illustrate the total station's long-term stability. By leveraging these tools, professionals can make informed decisions about instrument maintenance and replacement, ensuring consistent accuracy across various surveying projects.
Adjust Instrument Settings Based on Calibration Results
Adjusting instrument settings based on calibration results is crucial for maintaining total station accuracy. Surveyors analyze the calibration data to identify any deviations from the manufacturer's specifications and make necessary adjustments to the instrument's parameters. These adjustments may include corrections to the vertical and horizontal angles, distance measurements, and compensator settings.
Modern total stations often feature software-based calibration routines that guide users through the adjustment process. Surveyors input the calibration results into the instrument's software, which then calculates and applies the appropriate corrections. This automated approach ensures consistent and accurate adjustments across different instruments and operators.
After making adjustments, surveyors should perform verification measurements to confirm the effectiveness of the changes. This step involves measuring known points or baselines to validate the instrument's performance. By following this systematic approach to adjusting settings based on calibration results, surveyors can maintain the highest level of accuracy in their total station measurements.
Verify Accuracy in the Field After Calibration
Verifying accuracy in the field after calibration is crucial for ensuring total station reliability. Surveyors should conduct field checks on known points or baselines to confirm the instrument's performance under real-world conditions. This process helps identify any discrepancies between laboratory calibration and actual field measurements.
Field verification typically involves measuring distances and angles to established control points. Surveyors compare these measurements to previously recorded values, noting any deviations that exceed acceptable tolerances. This practice helps detect issues that may not have been apparent during the calibration process, such as environmental factors affecting instrument performance.
Regular field verification also serves as a quality control measure for surveying projects. By documenting and analyzing field check results, surveyors can demonstrate the reliability of their data to clients and stakeholders. This approach builds confidence in the accuracy of total station measurements and helps maintain high standards in surveying practices.
Employ Proper Setup for High-Precision Measurements
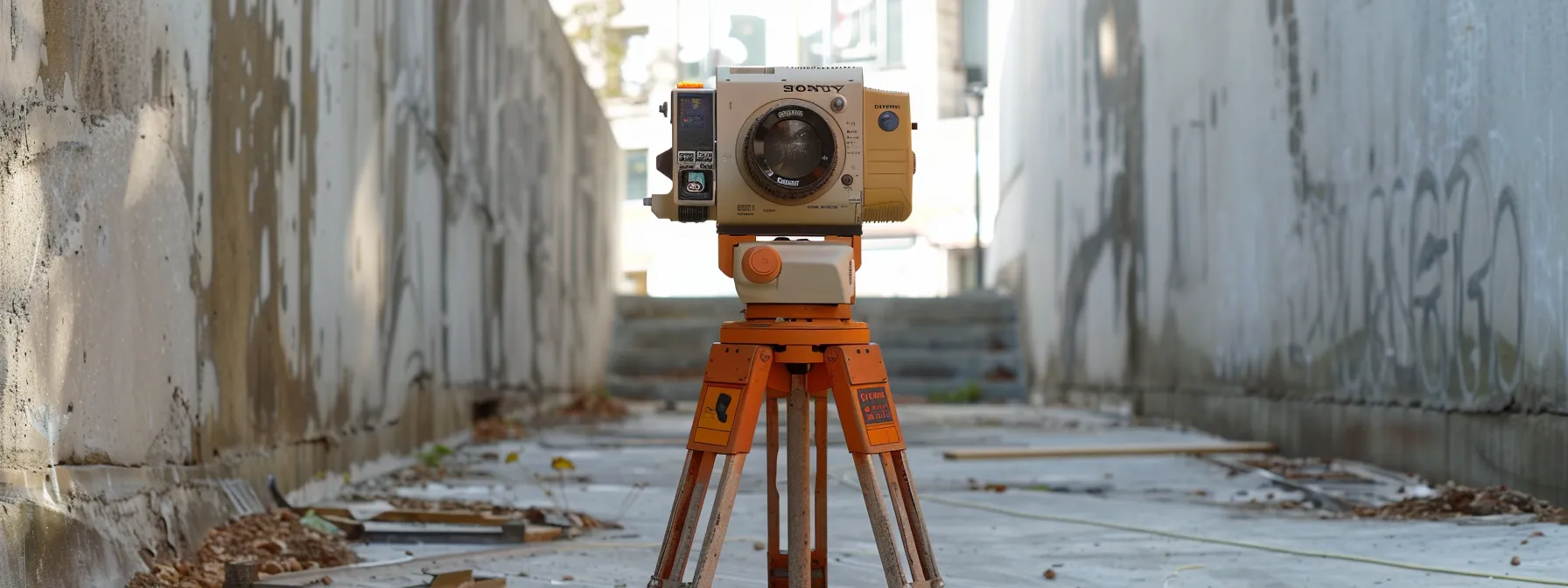
Proper setup is crucial for high-precision measurements with total stations. This section covers essential procedures including tripod and instrument setup, accurate centering, precise leveling, collimation error adjustments, correct orientation with backsights, and instrument stability verification. Following these steps ensures reliable data collection for surveying projects.
Ensure Proper Tripod and Instrument Setup Procedures
Proper tripod and instrument setup procedures form the foundation for accurate total station measurements. Surveyors must ensure the tripod legs are firmly planted on stable ground, with each leg adjusted to provide a level platform. The tripod head should be positioned at a comfortable height for the operator, typically around chest level, to minimize fatigue during extended surveying sessions.
Once the tripod is secure, surveyors carefully mount the total station onto the tribrach, ensuring a snug fit without overtightening. The instrument's optical plummet or laser plummet is then used to precisely center the total station over the survey point. This step is crucial for maintaining the instrument's position relative to known coordinates throughout the measurement process.
After centering, surveyors fine-tune the instrument's leveling using the tribrach's foot screws and built-in bubble levels. Modern total stations often feature electronic tilt sensors that provide real-time feedback on the instrument's orientation. Achieving proper leveling ensures accurate horizontal and vertical angle measurements, which are essential for high-precision surveying and construction layout tasks.
Accurately Center Instrument Over Survey Point
Accurately centering the total station over a survey point is crucial for precise measurements. Surveyors use optical or laser plummets to align the instrument's vertical axis with the ground point. This process ensures that the total station's position corresponds exactly to the known coordinates of the survey point, minimizing errors in subsequent measurements.
Proper centering techniques involve fine-tuning the instrument's position using the tribrach's adjustment screws. Surveyors should verify the centering accuracy by rotating the instrument 180 degrees and checking if the plummet remains on target. This method helps identify and correct any eccentricity errors that could affect the overall accuracy of the survey.
For high-precision work, surveyors often employ forced centering methods. This technique involves using specialized tribrachs or adapters that allow for quick and accurate instrument swaps without disturbing the centering over the survey point. Forced centering ensures consistency in instrument positioning throughout the survey, particularly when multiple setups are required.
Level the Total Station Precisely Before Measurement
Precise leveling of the total station is crucial for accurate measurements in surveying and construction projects. Surveyors use the instrument's built-in electronic bubble level or circular vial to achieve proper orientation. This process ensures that the vertical axis of the total station is perpendicular to the horizontal plane, minimizing errors in both horizontal and vertical angle measurements.
Modern total stations incorporate automatic compensators that correct for small leveling errors. However, surveyors should still manually level the instrument within the compensator's working range for optimal performance. This practice involves adjusting the tribrach's foot screws while observing the electronic level display, ensuring the instrument remains centered over the survey point.
After initial leveling, surveyors should verify the instrument's orientation by rotating it through 180 degrees. This check confirms that the leveling remains consistent across all directions, particularly important for high-precision measurements in engineering and monitoring applications. Regular level checks throughout the survey session help maintain accuracy, especially in environments prone to vibrations or temperature fluctuations.
Check and Adjust Instrument Collimation Errors
Checking and adjusting instrument collimation errors is crucial for maintaining total station accuracy. Surveyors perform this process by measuring horizontal and vertical angles to a distant target in both face left and face right positions. The difference between these measurements reveals any misalignment between the line of sight and the horizontal axis of the instrument.
Modern total stations often include built-in calibration routines that guide users through the collimation error check process. These routines typically involve taking multiple measurements to a well-defined target and automatically calculating the necessary adjustments. Surveyors should perform these checks regularly, especially before high-precision surveys or after transporting the instrument.
After identifying collimation errors, surveyors must apply corrections either manually or through the instrument's software. Some advanced total stations can store these corrections and automatically apply them to subsequent measurements. Regular collimation checks and adjustments ensure consistent accuracy across various surveying applications, from construction layout to topographic mapping.
Establish Correct Orientation With a Backsight
Establishing correct orientation with a backsight is crucial for ensuring total station accuracy in surveying projects. Surveyors select a known point with established coordinates as the backsight, typically a control point or benchmark. By sighting this reference point, the total station can calculate its position and orientation within the survey network, providing a foundation for subsequent measurements.
The backsight process involves carefully aiming the total station's telescope at the backsight target, often a prism or reflective marker. Surveyors input the known coordinates of the backsight point into the instrument's software, allowing it to compute the station's orientation. This step is critical for maintaining spatial accuracy throughout the survey, especially in large-scale projects where multiple instrument setups are required.
To verify the backsight's accuracy, surveyors often perform a check measurement to a second known point. This verification ensures that the initial orientation is correct and helps identify any potential errors in the setup process. Regular backsight checks throughout the survey session help maintain consistency and detect any instrument drift or environmental factors affecting measurement accuracy.
Confirm Instrument Stability Before Commencing Surveys
Confirming instrument stability is crucial before commencing surveys with a total station. Surveyors should allow the instrument to acclimate to ambient temperature and ensure it remains level throughout the setup process. This step prevents measurement errors caused by thermal expansion or contraction of the instrument's components.
To verify stability, surveyors can perform a series of quick measurements to a fixed target. By comparing these readings over a short period, they can detect any drift or inconsistencies in the instrument's performance. This practice is particularly important when working in areas prone to vibrations or on unstable ground conditions.
Modern total stations often incorporate electronic tilt sensors that continuously monitor the instrument's orientation. Surveyors should check these readings before and during the survey to ensure the instrument maintains its level position. Regular stability checks throughout the survey session help maintain data quality and reduce the need for time-consuming re-measurements.
Use Verification Techniques to Validate Field Data
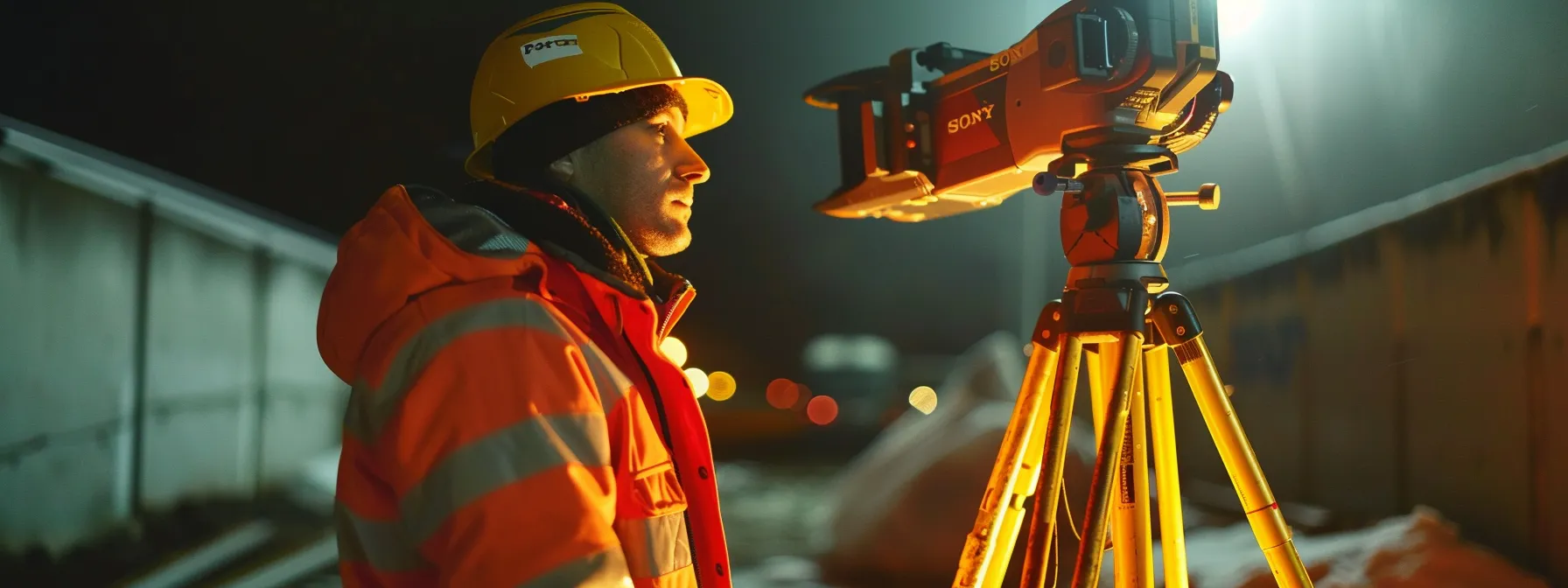
Verification techniques are essential for validating field data in total station surveys. This section explores methods to ensure accuracy, including repeated measurements, reciprocal observations, closed traverse surveys, baseline comparisons, redundancy techniques, and cross-checking with alternative instruments. These practices help surveyors detect errors and maintain high data quality throughout their projects.
Perform Repeated Measurements to Check Consistency
Surveyors perform repeated measurements to check consistency and ensure total station accuracy. This technique involves taking multiple readings of the same point or distance, allowing for the detection of random errors or instrument inconsistencies. By comparing these repeated measurements, surveyors can identify outliers and calculate the average value for more reliable results.
The number of repeated measurements depends on the required accuracy level and project specifications. For high-precision surveys, surveyors may take five to ten readings per point, while less critical applications might require only two or three repetitions. This approach helps minimize the impact of environmental factors such as atmospheric conditions or slight instrument movements.
To enhance the effectiveness of repeated measurements, surveyors should vary the instrument's face position between observations. This practice, known as "face left" and "face right" measurements, helps identify and compensate for systematic errors in the total station's optics or electronic components. By implementing consistent repetition protocols, surveyors can significantly improve the overall reliability of their field data.
Use Reciprocal Observations to Detect Errors
Reciprocal observations are a valuable technique for detecting errors in total station measurements. Surveyors perform these observations by measuring the same line or angle from both ends of a baseline. This method helps identify systematic errors in the instrument or environmental factors affecting measurement accuracy.
By comparing the results of reciprocal observations, surveyors can calculate the mean of the measurements and assess their consistency. Any significant discrepancies between the forward and backward measurements indicate potential errors that require further investigation. This approach is particularly useful for long-distance measurements where atmospheric conditions can have a substantial impact on accuracy.
To implement reciprocal observations effectively, surveyors should follow a structured procedure:
- Set up the total station at the first point and measure to the second point
- Move the instrument to the second point and measure back to the first point
- Compare the two sets of measurements for consistency
- Calculate the mean values if the differences are within acceptable tolerances
- Investigate and resolve any significant discrepancies before proceeding
Implement Closed Traverse Surveys for Validation
Closed traverse surveys are a crucial validation technique for total station accuracy. Surveyors use this method to create a series of connected measurements that begin and end at the same known point. By closing the loop, surveyors can calculate the error of closure, which provides a comprehensive assessment of the survey's overall accuracy.
Implementing closed traverses involves careful planning and execution. Surveyors must select appropriate station points, measure angles and distances between them, and record data meticulously. The final leg of the traverse should return to the starting point, allowing for a comparison between the measured and known coordinates.
Analysis of closed traverse data reveals valuable insights into total station performance. Surveyors calculate angular and linear misclosures, which indicate the cumulative errors in the survey. These results help identify systematic errors in the instrument or measurement process, enabling surveyors to make necessary adjustments and improve future survey accuracy.
Compare Measurements Against Known Baselines
Comparing measurements against known baselines is a critical verification technique for total station accuracy. Surveyors establish precise baselines with known distances and angles, typically using high-precision instruments or GPS technology. These baselines serve as reference standards for evaluating the performance of total stations in field conditions.
To implement this technique, surveyors measure the established baseline using their total station and compare the results to the known values. Any discrepancies between the measured and reference data indicate potential errors in the instrument's calibration or measurement process. This method allows surveyors to quantify the accuracy of their total station and make necessary adjustments.
Regular baseline comparisons help maintain consistent accuracy throughout surveying projects. Surveyors often perform these checks at the beginning and end of each survey day, ensuring that environmental factors or instrument drift have not compromised measurement quality. By incorporating baseline comparisons into their workflow, surveyors can confidently validate their field data and deliver reliable results to clients.
Apply Redundancy Techniques in Data Collection
Surveyors apply redundancy techniques in data collection to enhance total station accuracy and reliability. These methods involve taking multiple measurements of the same points or features from different instrument setups or angles. By incorporating redundant observations, surveyors can identify and mitigate errors, improving the overall quality of their field data.
One effective redundancy technique is the use of multiple backsights during station setup. Surveyors observe two or more known control points to establish the instrument's orientation, reducing the impact of individual measurement errors. This approach also allows for cross-verification of the instrument's position and helps detect any discrepancies in the control network.
Another valuable redundancy method is the observation of tie points between adjacent survey setups. By measuring common points from different instrument locations, surveyors create a network of interconnected observations. This redundant data allows for rigorous adjustment calculations, enhancing the precision of the final survey results and providing a robust framework for detecting and correcting measurement errors.
Cross-Check Data Using Alternative Instruments
Cross-checking data using alternative instruments is a crucial step in validating total station measurements. Surveyors often employ GPS receivers, laser scanners, or traditional leveling equipment to provide independent verification of their total station data. This approach helps identify any systematic errors or discrepancies in the primary measurements, ensuring the highest level of accuracy for critical surveying projects.
When implementing cross-checks, surveyors select a subset of key points measured by the total station and re-observe them using the alternative instrument. The comparison between these two sets of data allows for a comprehensive assessment of measurement quality. Any significant differences between the total station and alternative instrument readings prompt further investigation and potential recalibration of the primary equipment.
Regular cross-checks with alternative instruments also serve as a quality control measure for long-term projects. By periodically verifying total station data throughout a survey campaign, surveyors can detect and correct any drift in instrument performance or changes in site conditions. This practice enhances the overall reliability of the survey results and provides clients with confidence in the accuracy of the final deliverables.
Identify and Correct Common Total Station Errors

Identifying and correcting common total station errors is crucial for maintaining accuracy in surveying projects. This section explores methods to detect instrumental errors, recognize environmental factors, adjust for atmospheric effects, correct misalignments, mitigate human errors, and implement quality control procedures. By addressing these issues, surveyors can ensure reliable data collection and enhance overall measurement precision.
Detect Instrumental Errors and Apply Corrections
Detecting instrumental errors in total stations is crucial for maintaining measurement accuracy. Surveyors regularly perform checks to identify common errors such as collimation, horizontal axis tilt, and vertical index errors. These checks involve taking measurements in both face left and face right positions, comparing the results to reveal any discrepancies.
Once identified, instrumental errors can be corrected through a combination of mechanical adjustments and software calibration. Modern total stations often feature built-in calibration routines that guide users through the correction process. For older instruments, surveyors may need to manually adjust screws or apply correction factors to their measurements.
Regular error detection and correction procedures help maintain total station accuracy over time. Surveyors typically perform these checks before major projects or after transporting the instrument to ensure reliable data collection. By systematically addressing instrumental errors, surveyors can significantly improve the quality of their field measurements and final survey products.
Recognize Environmental Factors Affecting Accuracy
Environmental factors significantly impact total station accuracy, requiring surveyors to recognize and account for these influences. Temperature fluctuations can cause thermal expansion or contraction of the instrument's components, affecting measurements. Surveyors must allow the total station to acclimate to ambient conditions before beginning work and monitor temperature changes throughout the day.
Atmospheric conditions, including humidity and air pressure, affect the speed of light and consequently the accuracy of electronic distance measurements (EDM). Modern total stations often include built-in sensors to measure these parameters and apply corrections automatically. Surveyors should regularly verify these readings and manually input atmospheric data when necessary to ensure precise measurements.
Wind and vibrations can introduce errors by causing slight movements of the instrument or target prisms. To mitigate these effects, surveyors should use stable tripods and consider wind shields in exposed areas. Additionally, they must be aware of local sources of vibration, such as heavy machinery or traffic, and plan survey sessions accordingly. The following table summarizes key environmental factors and their impacts on total station accuracy:
Adjust for Temperature and Atmospheric Pressure Effects
Adjusting for temperature and atmospheric pressure effects is crucial for maintaining total station accuracy. Surveyors must input correct atmospheric data into the instrument to compensate for variations in the speed of light, which directly affects distance measurements. Modern total stations often feature built-in sensors that automatically measure these parameters, but manual verification is still recommended for high-precision work.
Temperature fluctuations can cause thermal expansion or contraction of the total station's components, potentially leading to measurement errors. Surveyors should allow the instrument to acclimate to ambient conditions before beginning work and monitor temperature changes throughout the survey session. For extended projects, periodic recalibration may be necessary to account for significant temperature shifts.
Atmospheric pressure also plays a vital role in total station accuracy, particularly for electronic distance measurements (EDM). Surveyors working at different elevations or in rapidly changing weather conditions must be especially vigilant in updating pressure readings. By consistently adjusting for temperature and atmospheric pressure effects, surveyors can significantly improve the reliability of their measurements and ensure high-quality data for various applications, from construction layout to topographic mapping.
Correct for Prism and Reflector Misalignments
Correcting for prism and reflector misalignments is crucial for maintaining total station accuracy. Surveyors must ensure that prisms are properly aligned with the instrument's line of sight to minimize offset errors. Regular checks of prism constants and careful mounting procedures help prevent these misalignments, which can significantly impact distance measurements.
Reflectorless measurements require special attention to surface characteristics and incidence angles. Surveyors should be aware that different materials and textures can affect the accuracy of reflectorless readings. By understanding these factors and adjusting measurement techniques accordingly, surveyors can improve the reliability of their data in situations where prism use is impractical.
To correct for misalignments, surveyors can employ techniques such as measuring to multiple prisms or using 360-degree prisms to reduce orientation errors. Additionally, performing regular calibration checks on prism offsets and applying appropriate corrections in the total station's software helps maintain measurement accuracy. By addressing prism and reflector misalignments systematically, surveyors can enhance the overall quality of their survey data.
Mitigate Human Errors in Data Recording Procedures
Mitigating human errors in data recording procedures is crucial for maintaining total station accuracy. Surveyors should implement double-entry systems, where measurements are recorded independently by two team members and cross-checked for discrepancies. This approach significantly reduces the risk of transcription errors and ensures data integrity throughout the survey process.
Modern total stations often feature integrated data collection software that minimizes manual input errors. Surveyors should familiarize themselves with these systems and utilize features such as automated point coding and attribute assignment. By leveraging technology to streamline data recording, professionals can focus on critical observation tasks and reduce the likelihood of human-induced mistakes.
Regular field checks and data verification procedures play a vital role in mitigating human errors. Surveyors should establish protocols for reviewing recorded data on-site, including comparing measurements to known control points and performing closure calculations. These real-time quality control measures allow for immediate error detection and correction, preventing small mistakes from compounding into significant inaccuracies in the final survey results.
Implement Rigorous Quality Control Procedures
Implementing rigorous quality control procedures is essential for maintaining total station accuracy. Surveyors should establish a comprehensive checklist that covers all aspects of data collection, processing, and analysis. This checklist should include regular instrument calibration checks, verification of control points, and systematic review of field notes and digital data.
A key component of quality control is the implementation of redundant measurements. Surveyors should perform multiple observations of critical points from different station setups, allowing for cross-verification and error detection. This approach helps identify outliers and ensures the reliability of the final survey results.
Regular peer reviews and external audits play a crucial role in maintaining high standards of total station accuracy. Surveyors should establish a system for independent verification of their work, including periodic assessments by experienced colleagues or third-party experts. This practice not only enhances the quality of individual projects but also contributes to continuous improvement in surveying techniques and procedures. The following table outlines key elements of a rigorous quality control process:
Maintain Total Station Equipment for Optimal Performance
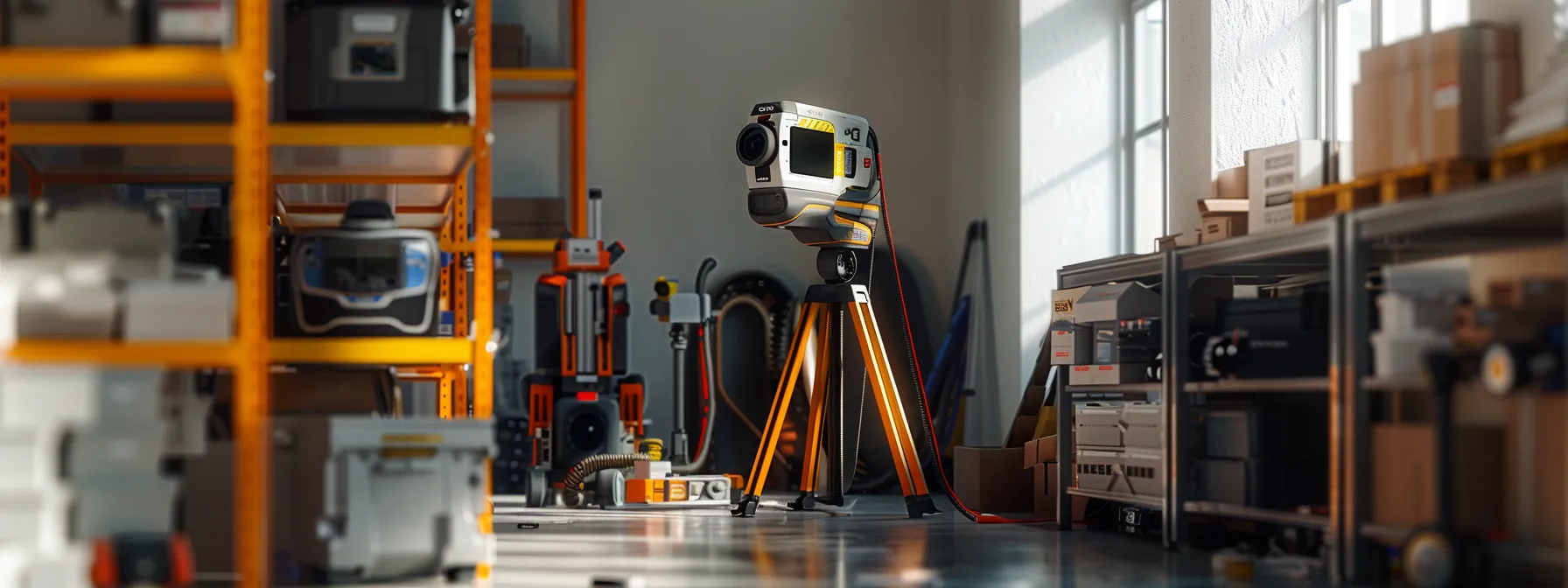
Maintaining total station equipment is crucial for ensuring optimal performance and accuracy. This section covers essential practices for equipment care, including proper cleaning and storage, regular component inspections, firmware updates, timely replacements, operator training, and professional servicing. By following these guidelines, surveyors can extend the lifespan of their instruments and maintain consistent measurement accuracy in the field.
Clean and Store Total Station Equipment Properly
Proper cleaning and storage of total station equipment are essential for maintaining accuracy and extending the instrument's lifespan. Surveyors should clean the total station after each use, removing dust and debris with a soft brush or lint-free cloth. Special attention should be given to the optical components, using appropriate lens cleaning solutions to prevent scratches or damage.
When storing the total station, surveyors must ensure it is placed in a padded, moisture-resistant case to protect it from environmental factors. The storage area should maintain a consistent temperature and humidity level to prevent condensation and thermal stress on the instrument's components. It is crucial to remove batteries during long-term storage to prevent corrosion and potential damage to the total station's electrical systems.
Regular maintenance of accessories, such as tripods, tribrachs, and prisms, is equally important for overall system accuracy. These components should be cleaned, inspected for wear, and properly stored alongside the total station. By implementing a comprehensive cleaning and storage routine, surveyors can ensure their equipment remains in optimal condition, ready for accurate measurements in the field.
Inspect Instrument Components on a Regular Basis
Regular inspection of total station components is crucial for maintaining instrument accuracy and reliability. Surveyors should establish a systematic routine for examining key parts, including the optical system, electronic components, and mechanical elements. This proactive approach helps identify potential issues before they escalate into major problems, ensuring consistent performance in the field.
Optical components, such as lenses and prisms, require careful inspection for scratches, dust, or misalignment. Surveyors should use specialized tools, like magnifying glasses or collimation testers, to detect subtle imperfections that could affect measurement accuracy. Electronic components, including the display, keypad, and data ports, should be checked for proper functionality and signs of wear or corrosion.
Mechanical parts, such as focusing knobs, leveling screws, and tribrach connectors, demand close attention during inspections. Surveyors must verify smooth operation and proper alignment, lubricating moving parts as needed to prevent wear and maintain precise adjustments. By conducting thorough component inspections regularly, professionals can significantly extend the lifespan of their total stations and ensure consistent accuracy across various surveying applications.
Keep Firmware and Software Updated for Accuracy
Keeping firmware and software updated is crucial for maintaining total station accuracy. Manufacturers regularly release updates that address bugs, improve functionality, and enhance measurement precision. Surveyors should check for updates periodically and install them promptly to ensure their instruments operate with the latest improvements.
Firmware updates often include calibration refinements and new features that can significantly impact total station performance. These updates may introduce advanced error compensation algorithms or optimize data processing capabilities. By staying current with firmware versions, surveyors can leverage these enhancements to achieve higher accuracy in their measurements.
Software updates for data collection and processing systems are equally important for maintaining total station accuracy. These updates may include improvements in coordinate transformations, adjustment calculations, or data export formats. Surveyors should establish a regular schedule for checking and installing software updates to ensure compatibility with the latest firmware and to take advantage of new accuracy-enhancing features.
Promptly Replace Any Worn or Damaged Components
Promptly replacing worn or damaged components is essential for maintaining total station accuracy. Surveyors should regularly inspect critical parts such as optical components, electronic modules, and mechanical assemblies for signs of wear or damage. By addressing issues immediately, professionals can prevent minor problems from escalating and affecting measurement precision.
Delaying component replacement can lead to cascading failures and compromise overall instrument performance. For instance, a worn tribrach may cause subtle misalignments that accumulate over time, resulting in significant errors across large survey areas. Surveyors should maintain a stock of common replacement parts and establish relationships with authorized service centers to minimize equipment downtime.
When replacing components, surveyors must ensure compatibility and proper installation to maintain total station accuracy. Using manufacturer-approved parts and following recommended procedures for replacement and calibration is crucial. After installing new components, professionals should perform comprehensive accuracy checks to verify that the instrument meets specifications before returning it to active field use.
Train Operators in Proper Equipment Handling
Training operators in proper equipment handling is crucial for maintaining total station accuracy. Surveyors should implement comprehensive training programs that cover all aspects of instrument setup, operation, and maintenance. These programs should emphasize the importance of careful handling, proper leveling techniques, and accurate data entry procedures to ensure consistent performance in the field.
Hands-on practice sessions are essential for developing proficiency in total station operation. Experienced surveyors should guide new operators through common field scenarios, demonstrating best practices for instrument setup, measurement techniques, and troubleshooting. Regular refresher courses help maintain skill levels and introduce operators to new features or updates in total station technology.
Proper equipment handling also involves educating operators on the potential consequences of mishandling. Surveyors should understand how small errors in setup or operation can propagate through measurements, affecting overall project accuracy. By fostering a culture of precision and care, survey teams can significantly reduce the risk of equipment damage and measurement errors, ultimately improving the reliability of their total station data.
Arrange Regular Professional Instrument Servicing
Arranging regular professional instrument servicing is essential for maintaining total station accuracy and longevity. Surveyors should schedule annual or bi-annual maintenance appointments with authorized service centers to ensure their equipment receives expert care. These professional servicing sessions involve comprehensive inspections, calibrations, and adjustments that go beyond routine field checks.
During professional servicing, technicians use specialized equipment to assess and fine-tune total station components. They perform detailed optical alignments, electronic calibrations, and mechanical adjustments to restore the instrument to factory specifications. This level of precision maintenance helps prevent cumulative errors and ensures consistent performance across various surveying applications.
Surveyors should maintain detailed records of professional servicing appointments and outcomes. These records serve as valuable documentation for quality assurance purposes and help track the instrument's long-term performance trends. By adhering to a regular professional servicing schedule, surveyors can maximize their total station's accuracy, reliability, and operational lifespan. The following table outlines key aspects of professional instrument servicing: